Loose impact attenuating surfaces
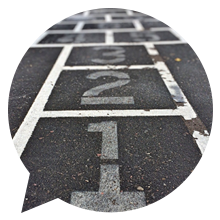
General
It is important for loose impact attenuating surfaces (LIAS) to be installed in accordance with the manufacturer's instructions.
EN 1176 sets out examples of specifications for LIAS.
One of the most common causes of unsatisfactory LIAS performance is inadequate simple maintenance. All play facilities and surfaces should be kept free from hazards. Play areas therefore need to be inspected and maintained on a regular basis.
The DCMS, the HSE and BSI recommend this inspections regime for play equipment and surfaces:
- A daily or weekly visual inspection
- A monthly or quarterly operational inspection
- An annual independent expert inspection
Bark
Bark from different tree species have quite different characteristics in terms of texture, performance and durability. The two most common types of bark used in the UK are:
- Granular bark - predominantly pine species (Pinus)
- Elastic or supple bark – predominantly spruce species (Picea)
Granular bark
Once laid the performance of granular particles contributes to the ability of the surface to be practically self-levelling when being played on. In areas of particularly high play activity weekly levelling with a rake is recommended.
In practice, the bottom 200mm of a 300mm layer of granular bark tends to naturally adhere together, to form a firm, yet yielding free drainage base. The top 50-100mm surface layer naturally remains loose and does not matt tightly. The upper surface "gives" easily under initial impact whilst the base layer tends to cushion the residual impact of any fall.
As the upper surface tends to wear, bark pieces of the lower layer will naturally become dislodged, to renew and maintain the surface layer.
The surface will gradually wear down depending on use. As LIAS have high impact absorbency resulting from the natural ability of the surface to "move" it is important to have readily available additional bark available to top up to the original level to ensure that the desired critical fall height rating is maintained.
Elastic or supple barks
The texture of these barks causes them to initially matt together, but their natural flat shape rather than granular particles causes them to consolidate very tightly together. They retain some of their impact absorbency but their drainage ability rapidly diminishes. Topping up is best carried out prior to "forking" or "turning" so that the whole surface, old and new, forms a homogenous mass of equal texture and consistency throughout. The new rejuvenated bark has most structure and when mixed with the older material will initially enhance the draining characteristics. Top-up as required and totally replace every third or fourth year. The essential need to "turn" the entire surface greatly increases the maintenance costs.
Wood products
There is a profusion of products available of varying species and particle sizes ranging from carefully graded conifer chips, conifer peelings to chopped up old pallets
The chosen product must be well graded to eliminate all dust and fine materials, large chunks and long thin slithers.
Properly graded wood chips perform in a similar manner to granular bark. The lower 200mm of a 300mm surface will loosely bond together, allowing good drainage. The upper 50-100mm will remain loose and to some extent be partially self-levelling. Heavy wear areas will need additional material to be raked in from the surrounding areas into any depressions usually on a monthly basis depending on use. Wood type products are less durable than bark. Their structure will rapidly degrade necessitating total replacement. Mixing old and new wood surfaces is not usually recommended.
Sand
Many different types of sand are available. However, unless the sand has been properly screened and washed, it is likely to stain children's clothes.
A suitable product should have rounded particle sizes between 0.2mm-2.0mm.
Sand is attractive to animals, particularly cats, so in built-up urban areas it must be inspected daily and cleaned with disinfectant if necessary.
Budget for total replacement or screening of all fines every 6 to 8 years.
Increased wear on timber equipment, painted surfaces, moving joints and bearings will occur.
Prepared for RoSPA by John Latter and Andy Chalmers, Melcourt Industries Ltd.